There are few industries which are as technologically advanced as the automobile industry.
Think back to how cars were 60 or even just 30 years ago and the improvements made to comfort, safety, and fuel efficiency are clear.
Today, almost all modern cars have anti-lock brakes, air conditioning, airbags, heated rear windscreens, and power steering. While top range models are supplied with catalytic converters, heated seats, parking assistance, driver drowsiness detection systems, heads up displays, and cruise control, to name but a few.
Older cars are more polluting, more dangerous, and less comfortable. While all the cars of tomorrow will be electric, self-driving, and one day, even flying.
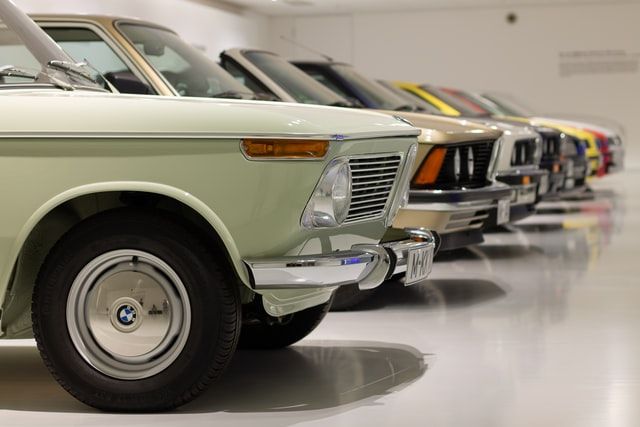
All of the changes made are thanks to the $101 billion that the global automobile industry invests in R&D each year. In 2020, a bad year for car sales thanks to the pandemic, Volkswagen alone invested $16 billion in research.
What is most significant for manufacturers and industry as a whole, is how much of this investment is going into the development of nanotechnology and how much the automobile industry depends on nanomaterials to make the improvements its customers demand.
“The virtue of using a nanocomposite for automotive applications is that less filler material is required to provide the same or better performance characteristics when compared to conventional materials,” explains Will Rodgers, a Staff Scientist at GM Research and Development. But the exploration of where nanomaterials can be applied is ongoing. “Our next applications for nanocomposite materials will be in exterior claddings, interior parts and in non-support trim,” Rodgers adds.
Nanomaterials are frequently employed because despite their low weight they remain incredibly strong. Weight reduction in automobile design is crucial, as it improves fuel efficiency which in turn decreases emissions and helps lessen environmental impact. Stronger parts also fail less, which makes them safer, and are more robust, which extends lifespan.
However, the ways that nanomaterials are used in manufacturing goes much further than just strong and light. To date, the list of nanotechnology applications in even low-end vehicles is far-reaching, as the advantages of using nanomaterials can be found in almost every part of a car.
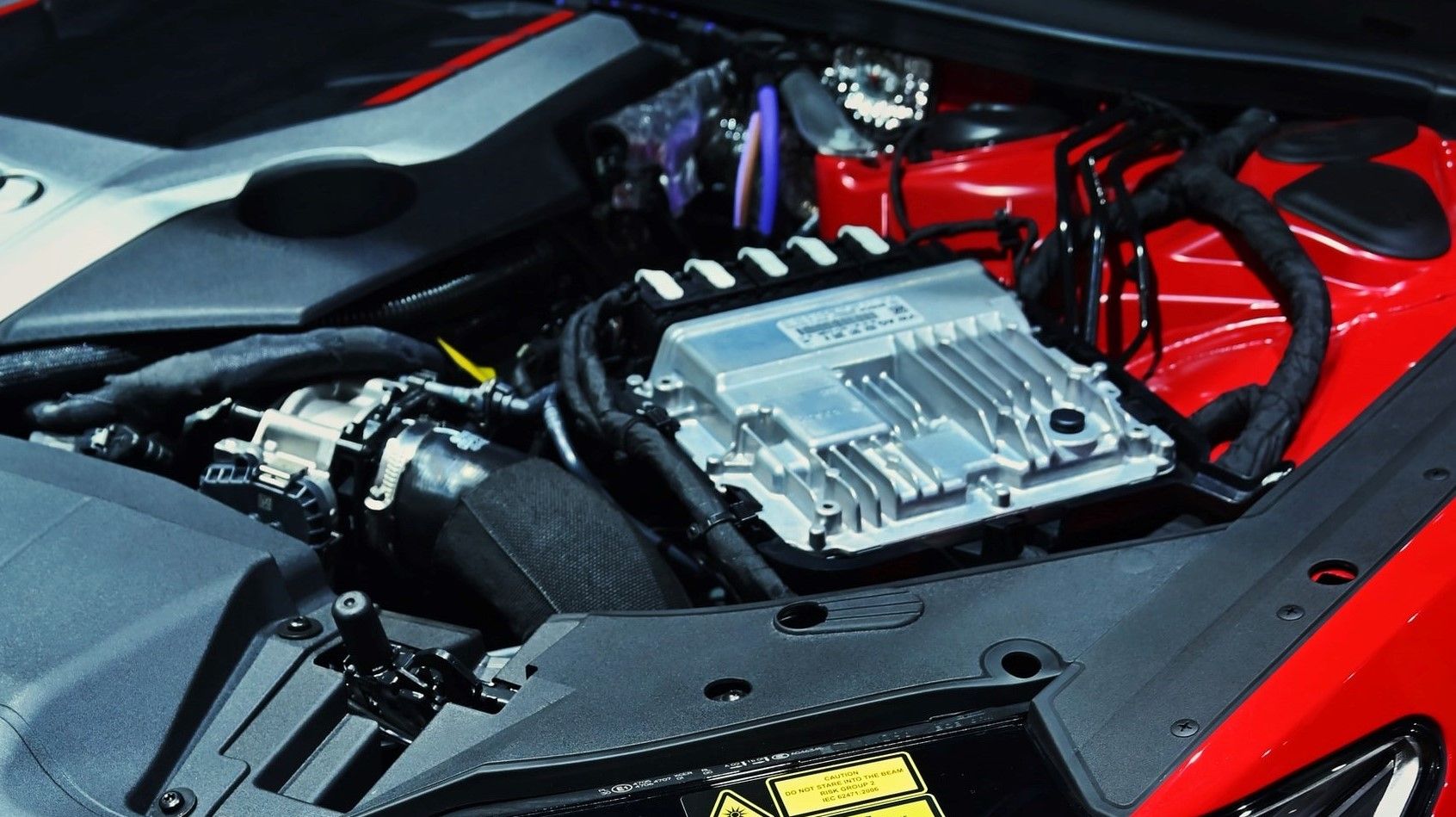
For example, the car tyres alone contain carbon nanofibres (CNF), fillers made from nano oxides (silica, alumina), as well as nanoclays. Other additives include graphene, Polyhedral Oligomeric Silsesquioxanes, and nanostructured Poly(alkylbenzene)-Poly(diene) (PAB-PDM). When combined, these industrial nano-ingredients improve traction and tyre lifespan, help maintain colour, reduce weight (improve fuel efficiency), and make the tyre electrically conductive to prevent the build up of static.
Nanomaterials are also used in the fluids that keep the car moving, improving braking systems, oils, and batteries. Modern car lubricants contain raw materials such as copper nanoparticles, graphene, nanostructured boric acid, and tungsten nanospheres.
Today, almost all fuel lines contain carbon nanomaterials with electro-static discharge capabilities to prevent static electricity from causing an explosion.
Textiles are often embedded with nanoparticles to help repel dirt, absorb sweat, increase wear resistance, reduce noise pollution, and provide anti-static and anti-microbial properties.
While the latest catalytic converters use more environmentally friendly nano-sized rhodium and palladium in ceramics to replace traditional metals such as cerium oxide and platinum.
Nanotechnologies such as spintronics (an understanding of how electrons operate in atoms) are also employed in more advanced vehicles to capture and reuse braking energy.
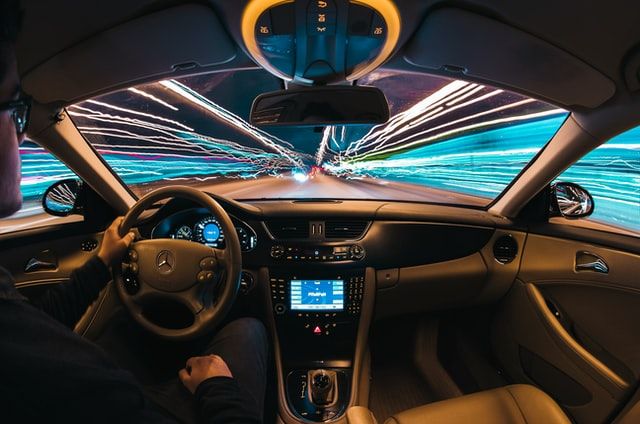
The automobile industry is truly embracing nanotechnology, and with good reason. In fact, a 2014 study conducted by researchers from the College of Engineering at the University of Miami, found, “A correlation exists in the automotive industry between the areas with increased nanotechnology incorporation and those with increased profit margins via improvements and customer demands.”
Given the expertise that the automobile industry applies to car design and the raw materials they use, as well as the rigorous safety testing new cars must go through, there can be little doubt that nanomaterials are safe and provide clear benefits to manufacturing.
Through better performance, cost savings, increased durability, improved safety, and for environmental reasons, nanotechnology now plays a key role in car and truck production.
And that’s relevant, because, if Ford, Tesla, VW, GM, Ferrari, Porsche, Tata, Lamborghini, Nissan, Peugeot, and Dacia are all using nanomaterials, maybe it’s time for other manufacturers to sit up and take note.
If you would like to learn more about how nanotechnology can improve the manufacture of plastics, resins, and coatings, visit NANO CHEMI GROUP.
Photo credit: Unsplash, Cenk Batuhan Özaltun on Unsplash, C Joyful, & Clay Leconey