The big problem with graphene is that it is so expensive. As an incredibly strong, yet incredibly light material, it has so many potential applications, yet its price makes so many of these possibilities not financially viable.
But now a team of nanotechnology researchers have found a completely new way to produce graphene; making it much quicker, much cheaper to make, by using any raw material that contains carbon. This means that coal, biochar, coke, car tyres, waste plastic, and even old food are now practical sources of graphene.
The new method was discovered by James Tour, a Professor of Chemistry, Material Science, and Nanotechnology, and his colleagues at Rice University, and produces atomically-thin sheets given the name ‘Flash Graphene’ due to the speed of the process and the bright light made during manufacturing.
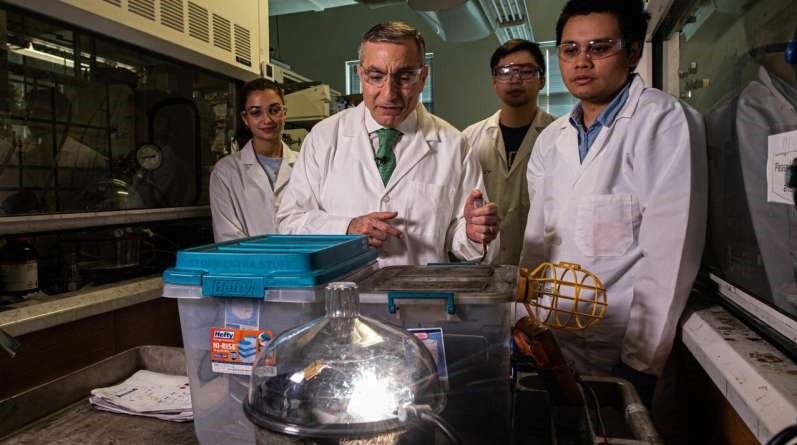
As the university press release explains, “… flash graphene is made in 10 milliseconds by heating carbon-containing materials to 3,000 Kelvin (about 5,000 degrees Fahrenheit).”
However, the heat is all focused on the reaction, very little of it is wasted. “All the excess energy comes out as light, in a very bright flash,” says Tour, “You can put your finger right on the container a few seconds afterwards. And keep in mind this is almost three times hotter than the chemical vapor deposition furnaces we formerly used to make graphene, but in the flash process the heat is concentrated in the carbon material and none in a surrounding reactor. And because there aren't any solvents. It's a super clean process.”
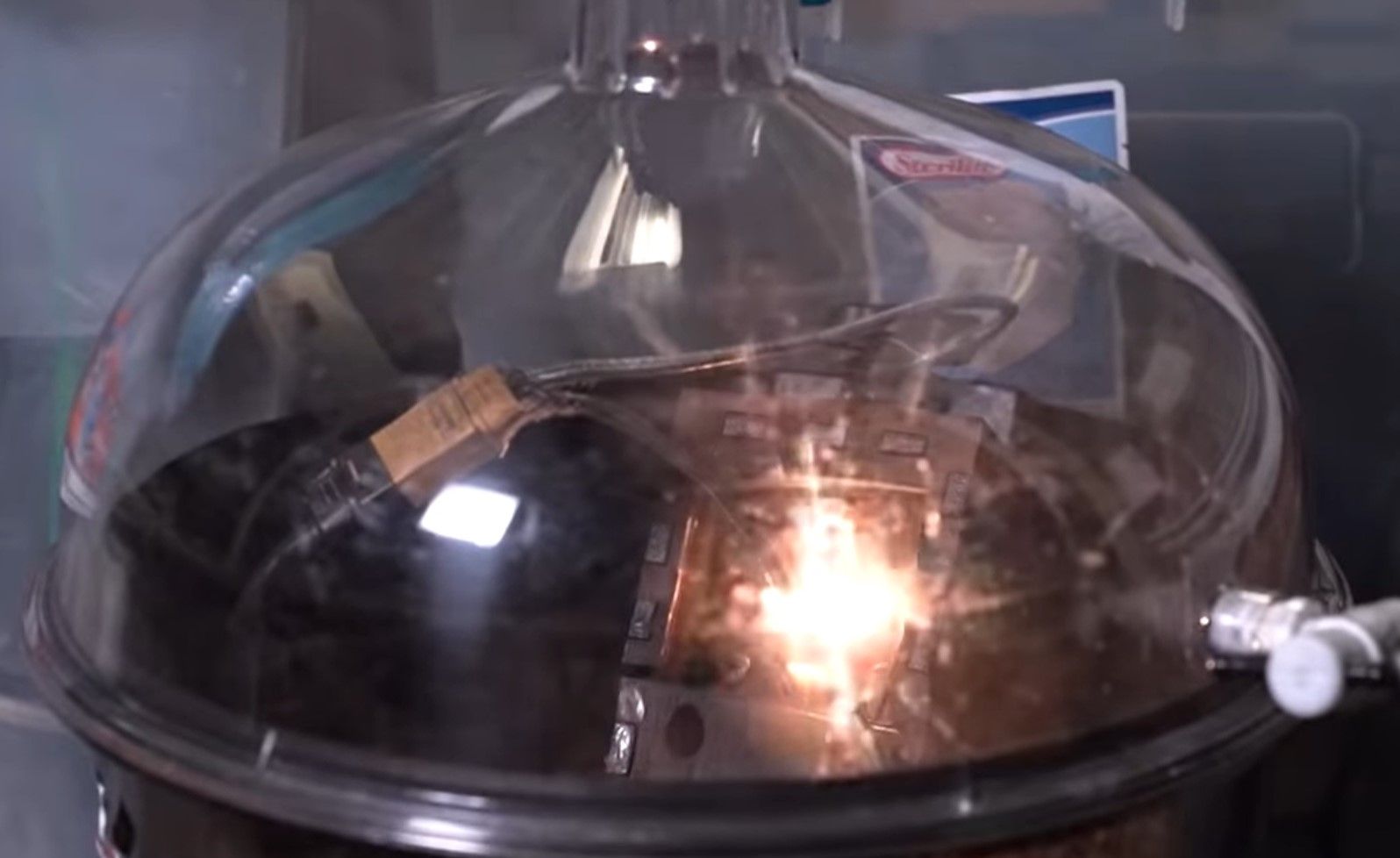
The team have now published their results in the journal Nature, where they explain how, “Most bulk-scale graphene is produced by a top-down approach, exfoliating graphite, which often requires large amounts of solvent with high-energy mixing, shearing, sonication or electrochemical treatment.”
Meanwhile, “Bottom-up synthesis of high-quality graphene is often restricted to ultrasmall amounts if performed by chemical vapour deposition or advanced synthetic organic methods, or it provides a defect-ridden structure if carried out in bulk solution.”
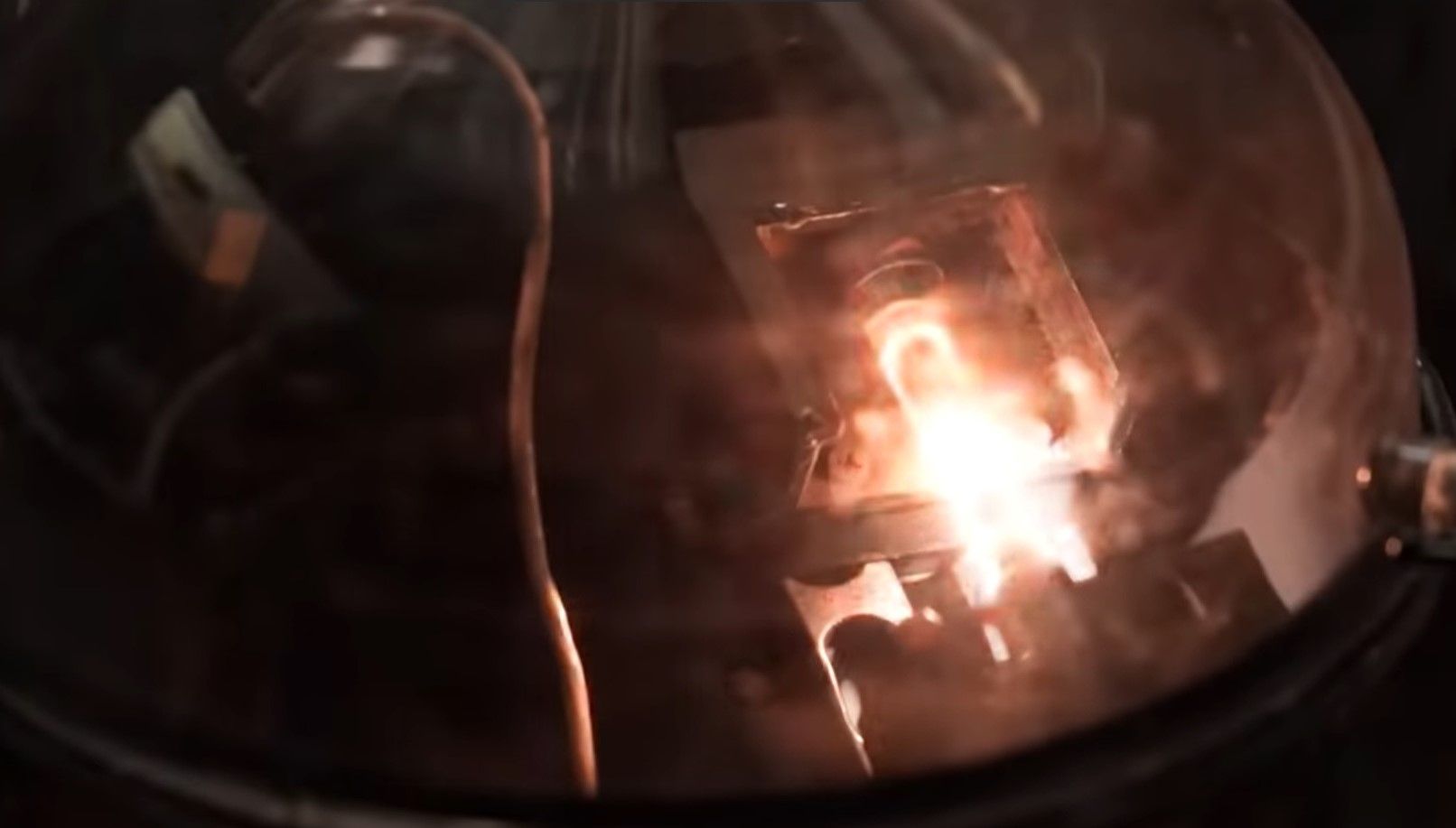
Instead, the researchers have now provided a new approach, stating that, “… flash Joule heating of inexpensive carbon sources - such as coal and mixed plastic waste - can afford gram-scale quantities of graphene in less than one second.”
“This is a big deal,” says Tour. “The world throws out 30% to 40% of all food, because it goes bad, and plastic waste is of worldwide concern. We've already proven that any solid carbon-based matter, including mixed plastic waste and rubber tires, can be turned into graphene.”
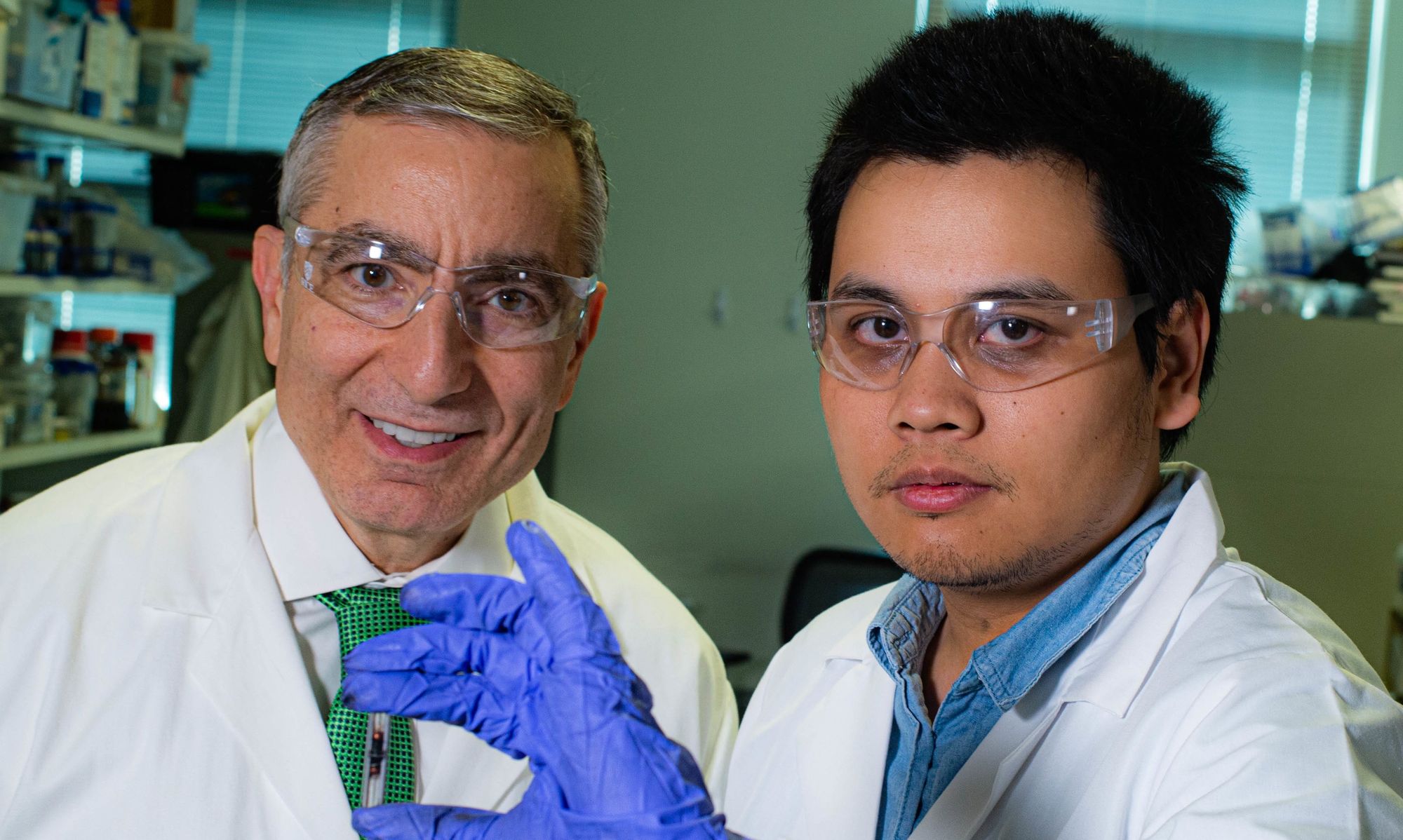
In addition, the study notes how the ‘Flash Graphene’ produced can be of good quality. “Yields depend on the carbon content of the source; when using a high-carbon source, such as carbon black, anthracitic coal or calcined coke, yields can range from 80 to 90 per cent with carbon purity greater than 99 per cent.” Adding that, “No purification steps are necessary.”
Significantly, from an engineering perspective, the graphene produced is of a highly practical form.
Most processes, such as exfoliation from graphite and chemical vapor deposition (CVD) make a type of graphene known as AB – Stacked. While this graphene can be of good quality, it can be hard to separate the individual layers. However, the new method makes ‘turbostratic’ graphene, which comes in layers that are misaligned with lower adhesion, they are easy to take apart. As a result, they separate in simple solvents or just come apart when mixed in composites.
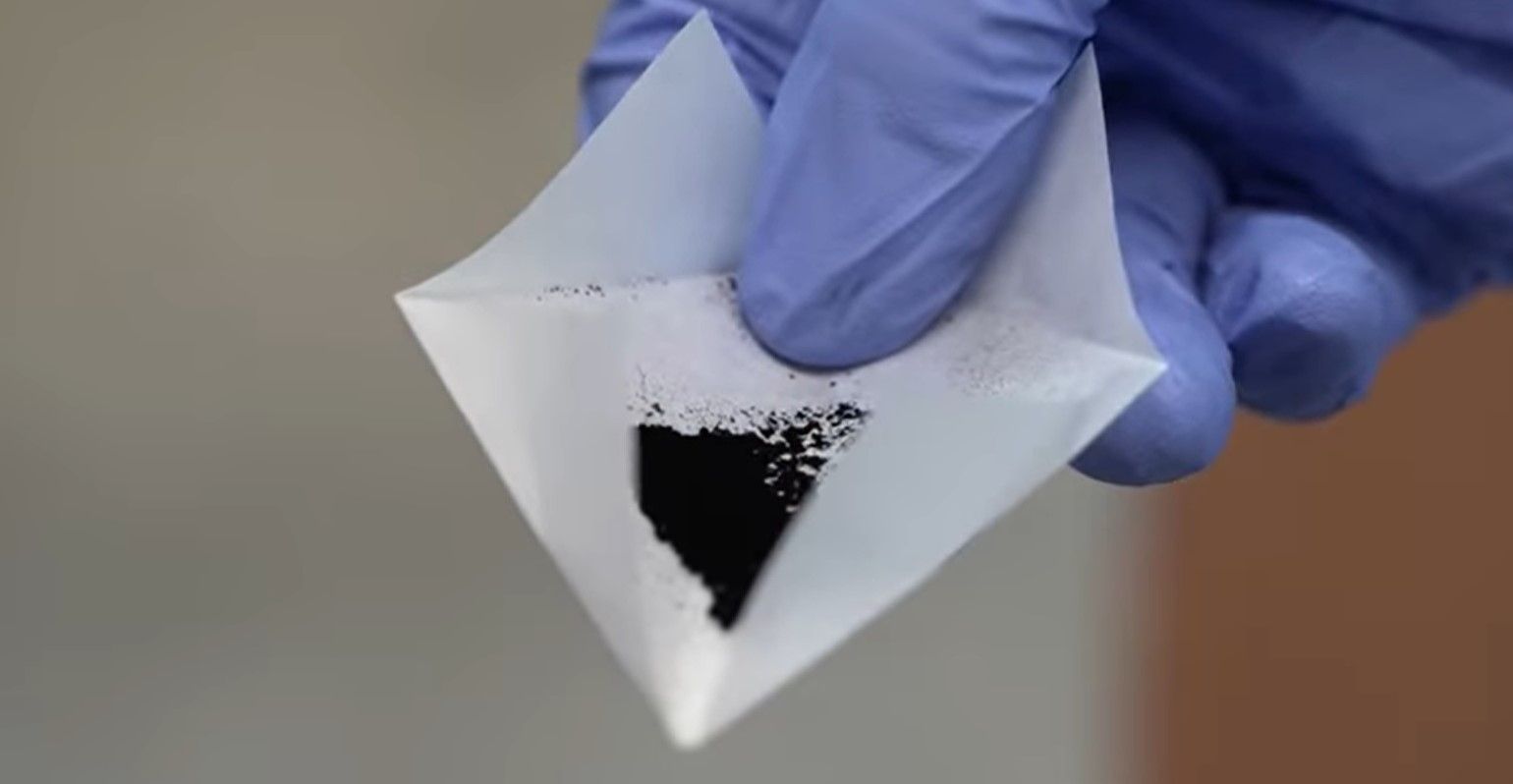
“That's important,” observes Tour, “because now we can get each of these single-atomic layers to interact with a host. With the present commercial price of graphene being $67,000 to $200,000 per ton, the prospects for this process look superb.”
This is because Flash Graphene looks likely to be a much cheaper mass production process than any previous approach. “The electric energy cost for Flash Graphene synthesis is only about 7.2 kilojoules per gram,” the report claims, “which could render Flash Graphene suitable for use in bulk composites of plastic, metals, plywood, concrete and other building materials.”
A fact supported by Tour when he outlines how in the past, “… graphene has been too expensive to use in these applications. The flash process will greatly lessen the price while it helps us better manage waste.”
This could make graphene a true game-changer in all manner of industries, as well as helping economies become more carbon neutral.
As an example, Tour believes that a concentration of just 0.1% of Flash Graphene added to cement could improve concrete strength by 35%. This means that much less concrete could produce the same strength.
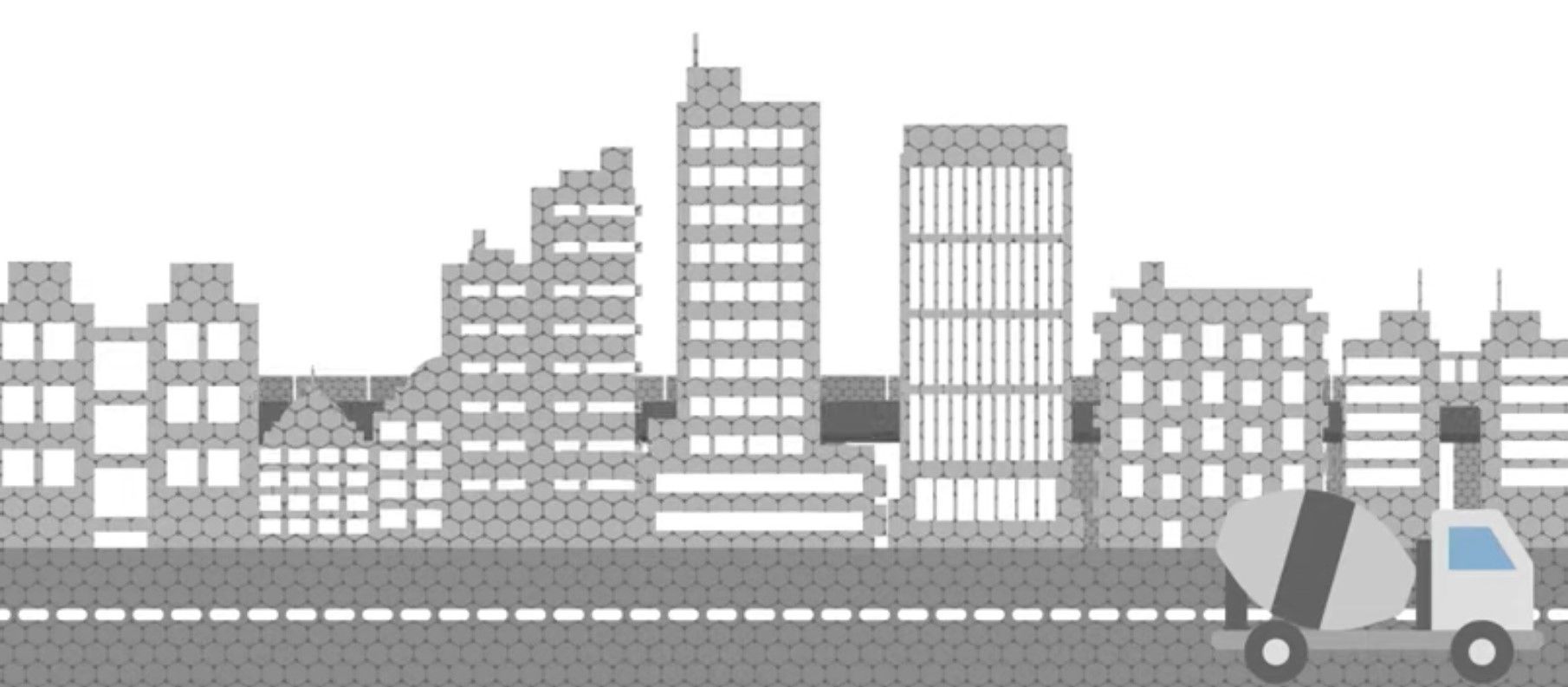
“By strengthening concrete with graphene, we could use less concrete for building, and it would cost less to manufacture and less to transport,” notes Tour. “Essentially, we're trapping greenhouse gases like carbon dioxide and methane that waste food would have emitted in landfills. We are converting those carbons into graphene and adding that graphene to concrete, thereby lowering the amount of carbon dioxide generated in concrete manufacture. It's a win-win environmental scenario using graphene.”
With concrete production accounting for 8% of man-made CO2 emissions, Flash Graphene is a major breakthrough.
The environmental advantages are not lost on the study’s co-author Asst. Prof. Rouzbeh Shahsavari. “Here, graphene acts both as a 2-D template and a reinforcing agent that controls cement hydration and subsequent strength development,” she says. “Turning trash to treasure is key to the circular economy.”
“With our method,” notes Tour, “the carbon becomes fixed. It will not enter the air again.” In addition, “When this process is industrialized, elements like oxygen and nitrogen that exit the flash reactor can all be trapped as small molecules because they have value.”
The team are now continuing their studies to examine how Flash Graphene operates when used as a raw material additive in plastics and concrete. They are also examining the practicality of up scaling the flash production process, but are confident that this relatively simple procedure could be reproduced on an industrial scale.
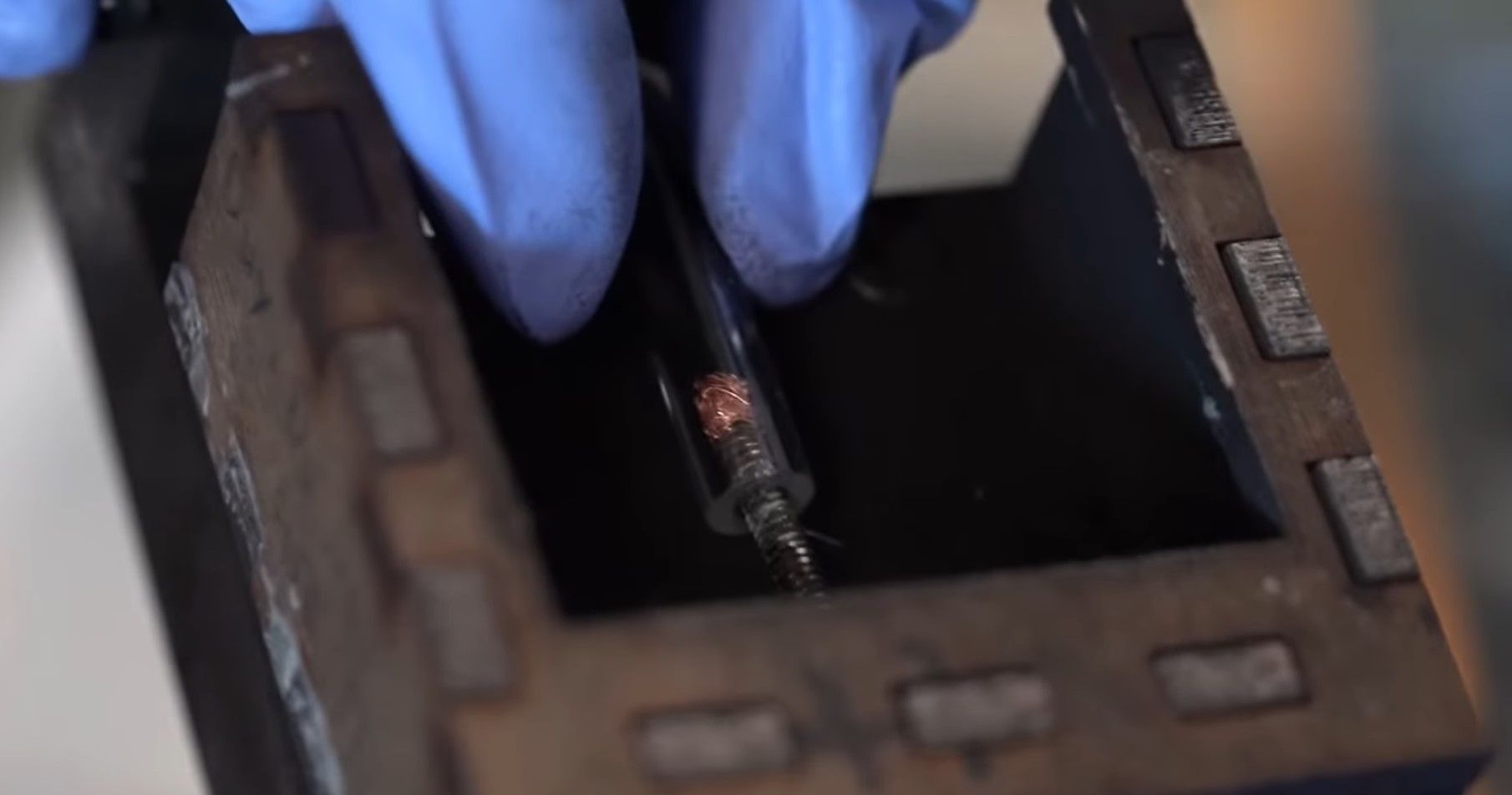
With this in mind, the team have set themselves the target of producing a kilogram of Flash Graphene a day in two years’ time and have begun a U.S. Department of Energy project to use coal as a feedstock.
“This could provide an outlet for coal in large scale by converting it inexpensively into a much-higher-value building material,” notes Tour.
But more than that, it may allow graphene to become the raw material that manufacturing was promised when it was first discovered. A strong, light, flexible ‘dream’ material with exceptional properties. For if the secret of producing graphene quickly and at low cost has now been found, then those promises may finally be fulfilled.
You can learn more about the process of 2D material manufacture and Flash Graphene’s discovery by watching this Rice University video on You Tube.
While here Prof. James Tour explains how Flash Graphene could make the world Plastic Neutral.
Photo credit: Rice University, & YouTube