Electrostatic discharge is expensive.
Recent estimates found that losses from ESD, in the electronics industry alone, ranged from $500 million to $5 billion each year.
This figure is understandable, given how little friction is required to make electrostatic.
Electrostatic Discharge is Easily Created
While the level of humidity in an environment has a big impact on the generation of electrostatic, a report published by the Electrostatic Discharge Association found that simply walking across carpet or vinyl tile can produce as much as 35,000 V of unwanted electrical charge.
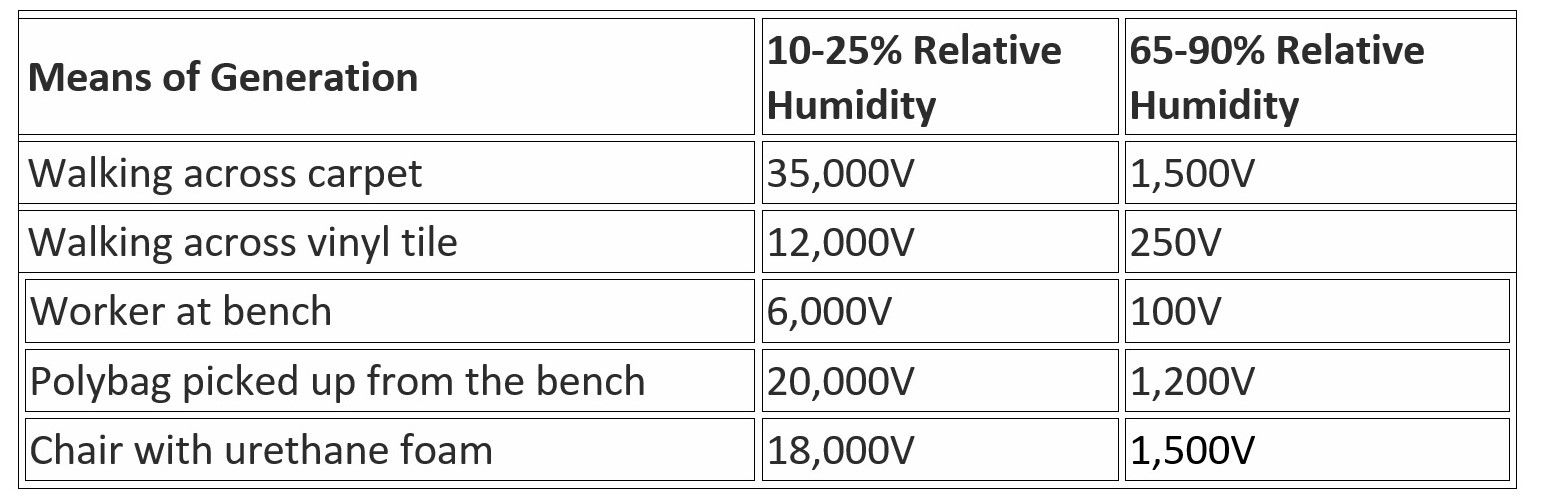
The report noting that, “An electrostatic charge may also be created on the material in other ways, such as by induction, ion bombardment, or close contact with another charged object. However, triboelectric charging [from contact] is the most common.”
While some of the damage caused by ESD is easily fixable, perhaps only a few cents to replace a diode, other components can cost hundreds of thousands of dollars to access and repair. Worse still is that priceless data can also be lost if the discharge hits electronic storage devices.
The problem for electronics manufacturers and users is exacerbated because many electrical components can be damaged at voltage levels as low as 100 volts, with some disk drive components affected by discharges of only 10 volts.
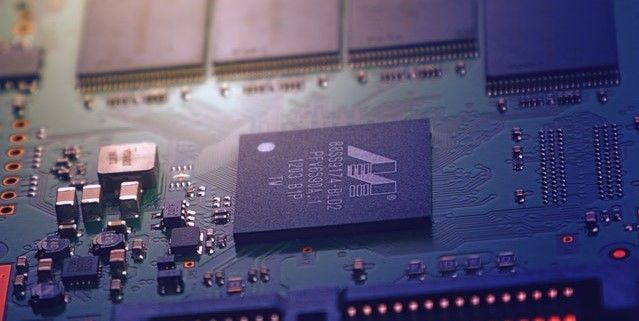
Furthermore, as devices become smaller, packing more and more circuitry into a tighter space, the general sensitivity of everyday objects to ESD is increasing.
Understanding these risks, manufacturers of consumer products, architects for light industrial buildings, offices, logistics parks, and storage spaces, as well as vehicle manufacturers are demanding materials that are better able to prevent ESD.
This has led material researchers to take a closer look at how to limit electrostatic build-up.
Electrostatic Discharge is Easy to Restrict
The greatest challenge in limiting ESD, is that it is present in every material. While polymers and other synthetic substances may be most closely associated with static electricity, silk, satin, rabbit fur, and even water can all generate a charge which may cause problems.
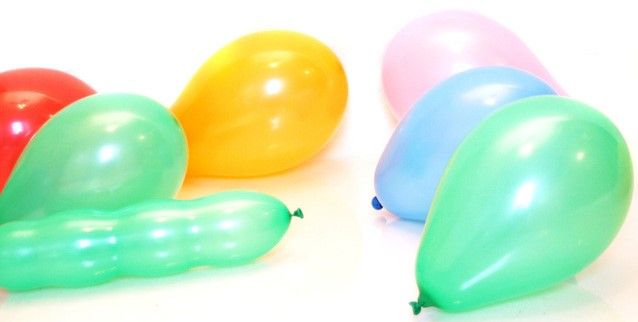
While simple earthing with wiring may be a solution in some instances, many researchers have found that nanotechnology can provide the most practical answer.
By applying nanomaterials evenly throughout a material in the production process, manufacturers have found a way to disperse any electrical charge before it builds up. It is a cost-effective solution for use in a wide range of materials.
A Solution to ESD
One company that has taken this technology and turned it into a practical, commercial product is NANO CHEMI GROUP.
Based in Prague in the Czech Republic, the company has been working on a variety of nanotechnology-based applications for inclusion in industrial materials since 2017. During this time, it has created products for use in polymers, resins, and coatings.
Their product range includes NANO AC PES-17, a polyester resin (isophthalic resin) based concentrate which contains 0.2 – 0.5 wt.% of carbon nanomaterials.
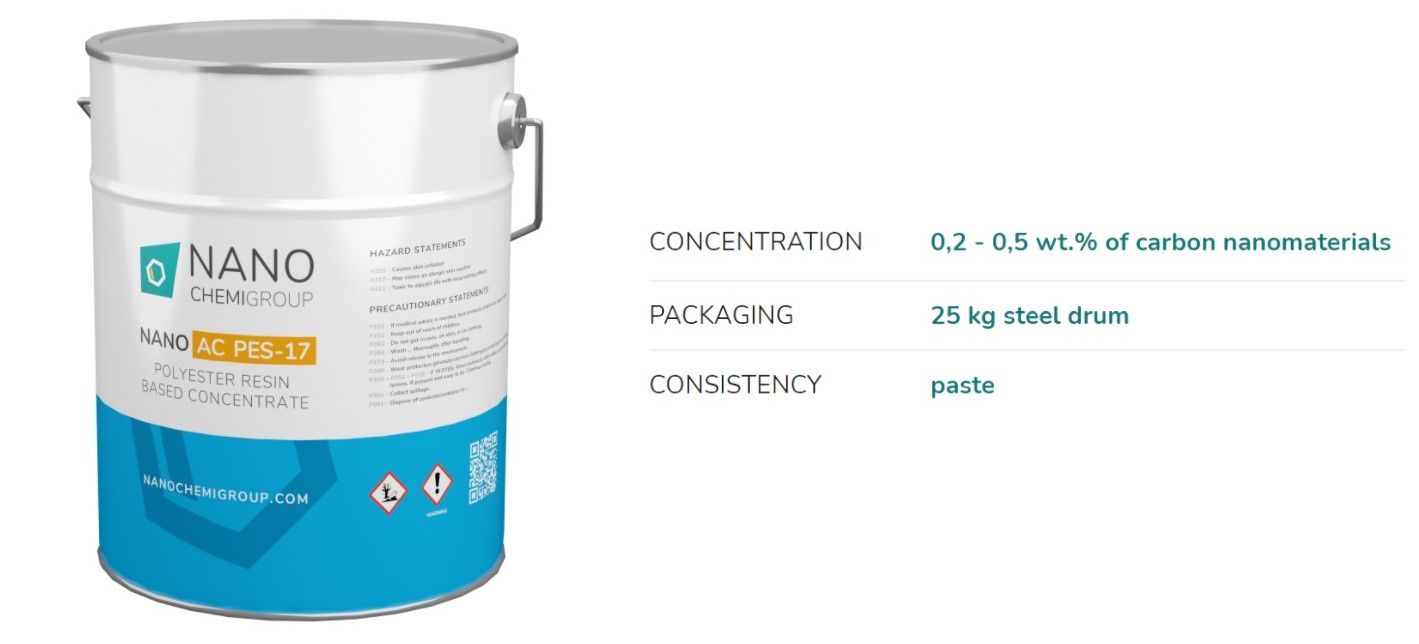
It is a specialized industrial additive has been produced for use in the manufacture of fibreglass and carbon composites, printing rollers, and in the production of electrostatic discharge (ESD) and antistatic discharge flooring, paints, and coatings.
Using NANO AC PES-17 can provide your products with increased:
· electrical conductivity
· thermal conductivity
· abrasion resistance
· chemical resistance
· mechanical strength
Understanding that ESD is a growing issue in an ever-wider range of industries and materials, NANO CHEMI GROUP (who sponsor this website) is also able to offer tailor-made solutions using nanotech that can be designed to order.
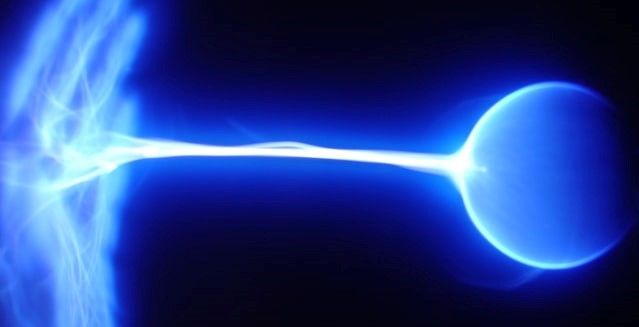
With a Nanomaterial Research Centre expected to be completed by late 2021, the company will be able to devise, sample, test, and manufacture industrial quantities of nanomaterial-based products that can add specific properties desired by its clients.
In this way, polymer manufacturers, resin suppliers, and the producers of other industrial materials are able to adapt their products to suit the exacting needs of their end-users. Improving the quality of their end product, while also saving money.
Photo credit: Jeff Hire, Amos, Denise Docherty, Johannes Plenio, & NANO CHEMI GROUP