Epoxy resins are used to build interesting objects like aircraft and snowboards, bicycles and cars. They are also used to build practical objects, like floor coverings, plastics, and coatings.
But why would anyone want to add nanoadditives to the mix?
What can a nanomaterial do for an epoxy resin?
The versatility of epoxy resins is based on their wide range of properties. They can be transparent or opaque, they can be rigid or flexible, and because they are excellent insulators, they are widely used in the electronics industry to prevent short circuiting as well as to protect against moisture and dust.
They are also strong and relatively cheap.
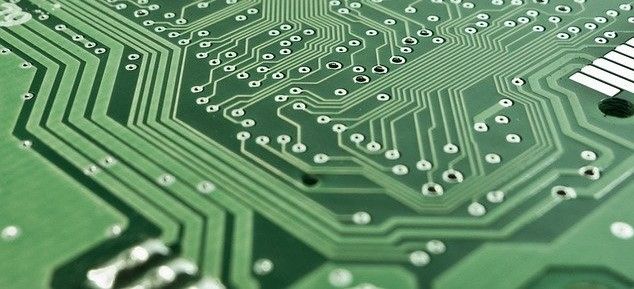
However, epoxy resins still have their short comings. For this reason, manufacturers are discovering the benefits of adding nanomaterials to provide missing properties, such as extra strength, electrical conductivity, scratch resistance, hardness, thermal conductivity, corrosion resistance, and chemical stability.
Each nanomaterial can provide a new property or even a combination of properties. Their shape, size, structure, and material substance impacting their raw material powers.
But what distinct advantages can specific nanomaterials provide?
Nanoclays
Nanoclays were originally used in making thermoplastics, but their versatility of properties has now spread to their use in epoxy resins. Here they can work as thermal stabilizers and pollutant removers, also potentially including flame retardancy and biocompatibility. They also add electrical and optical properties, and when deployed in fibre-reinforced plastic (FRP) can enhance corrosion resistance and mechanical strength.
One of the most commonly used nanoclays are halloysite nanotubes (HNTs) which are made from an aluminosilicate clay (Al2Si2O5(OH)4).
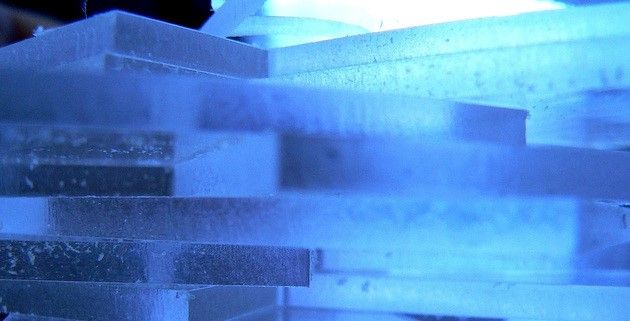
Aluminium nanoparticles
Nano-Al2O3 is perhaps the most widely used nanoparticle additive in the manufacture of polymer nanocomposites. Their popularity stems from the enhanced thermal and mechanical properties they provide, as well as their lower costs compared to nanotitania and carbon-based nanofillers.
Zinc Oxide Nanoparticles
ZnO-based nanofillers are used to increase surface hardness and corrosion resistance in epoxy matrices.
Iron Oxide Nanoparticles
With particles ranging in size from 10 to 50 nm and with a wide variety of names (such as ferrous ferric oxide or magnetite), nanoparticles of Fe3O4 have been found to add magnetic properties in epoxy-based nanocomposites. These properties are useful in creating micro-sensors, microwave absorbing elements, microelectromechanical devices, and systems which store or harvest energy.
Titanium Dioxide Nanoparticles
TIO2 nanoparticles, also commonly called Titania are nanoadditives designed for coatings. They are popular fillers as they add chemical stability and high corrosion resistance, without adding toxicity or a higher price.
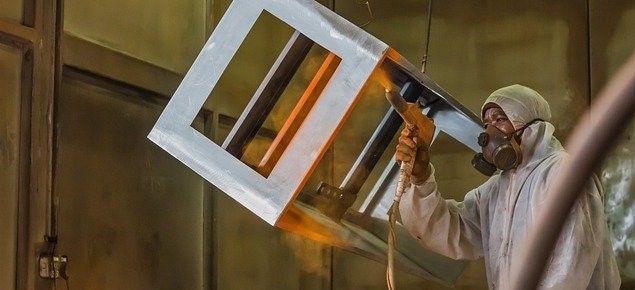
Silicon Dioxide
Also known as silica, nanoparticles of SiO2 (typically measuring 10 to 30 nm in diameter add the much sought-after properties of scratch, abrasion, and corrosion resistance to epoxy-based metal coatings.
Furthermore, nanosilica can be used to create ‘nanostructured organic–inorganic (O–I) “hybrid” systems’.
As a recent review of ‘Advances and Trends of Nanofilled/Nanostructured Epoxies’ published in the journal Materials explains, “[These systems] can be formed directly in the epoxy network during its development, with a morphology consisting of co-continuous organic domains chemically linked to the inorganic phase.” The synergy derived from combining nanosized phases into a bulk epoxy, is highly advantageous, providing different, “chemical composition, physical properties, and morphology of the final phases.”
They are often deployed in the production of ‘cold-cured’ adhesives, those which can set and harden in ambient temperatures.
Phosphorus-Based Nanofillers
Phosphorus compounds may be applied at the nanoscale to epoxy resins to increase their resistance to fire. When burning, they produce little smoke, form a stable carbonaceous (char) layer that helps restrict a fire’s spread, and due to their low toxicity, work as a halogen alternative.
Carbon-Based Nanofillers
Carbon-based nanofillers include a wide family of nanomaterials generally used at low concentrations to provide a mix of desirable properties, such as excellent physical and mechanical characteristics, hardness, high thermal conductivity, chemical stability, and biocompatibility.
They are often included in the manufacture of epoxy resins used to make flooring, as carbon nanomaterials can add the electrical conductivity needed to make antistatic flooring (ASD) or electrical static flooring (ESD). Since polymers intrinsically function as insulators, the application of nanomaterials can give them this much sought-after property.
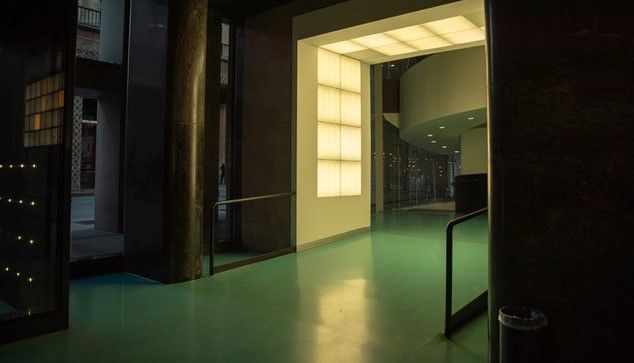
This sub-section of nanomaterials includes:
· Graphene
Most commonly graphene oxide (GO) due to its lower cost compared to carbon nanotubes while still adding strength, thermal and electrical conductivity, among other properties.
· Carbon nanotubes (CNTs)
Either single-walled (SWCNT) or multi-walled (MWCNT), carbon nanotubes are a popular additive to epoxy resins due to their low density and high aspect ratio which allows them to influence the chemical functionality of a material at very low concentrations (0.1–0.2 wt.%). Less nanomaterial is typically desirable to minimise self-aggregation.
CNTs are also a popular choice for the production of fibre-reinforced polymer (FRP) composites.
· Nanodiamonds
NDs are used in epoxy resins to enhance the mechanical properties, as well as boost the friction resistance and durability of a composite. They can also improve fracture resistance and thermal conductivity with as little as 0.5 wt.%.
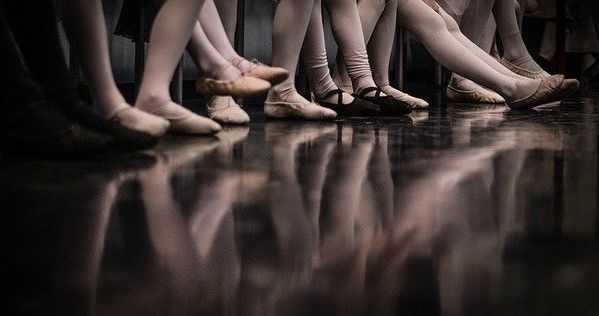
While this list of nanomaterials that can be applied to epoxy resins is not exhaustive, it does give a glimpse of the enormous range of properties that can be added if the correct raw material is chosen.
Furthermore, with nanotechnology researchers consistently making great strides, there is great potential for additional properties to be developed.
For now, though, epoxy resins are being manufactured with a variety of nanoadditives, both off-the-shelf commodities which provide a decent improvement of final products, but also custom-made nanoadditives which grant exacting qualities for epoxy resin users to pass on to their customers.
If you would like to know more about how nanomaterials can improve your epoxy resin products, especially ESD and ASD floorings, then please take a look at NANO CHEMI GROUP's product range.
Photo credit: Emiliano Fanti on Unsplash, Logan Stone on Unsplash, Pixabay, Michael Schwarzenberger from Pixabay, Dewald Van Rensburg from Pixabay, & Freeimages