Changing the properties of a material can be easy. Simple chemistry can work out which chemicals should be mixed in a solution to make it stronger, more flexible, more rigid, or more chemically resistant. Dyes can be used to add colour, or other chemicals added to increase durability.
With the manufacture of modern synthetic fibres, the chemistry becomes a lot harder, as the polymer melt and its additives must also be suitable for the electrospinning process.
Much of this challenge has now been solved with the development of nanotechnologies that can apply desirable properties to even the finest fibres.
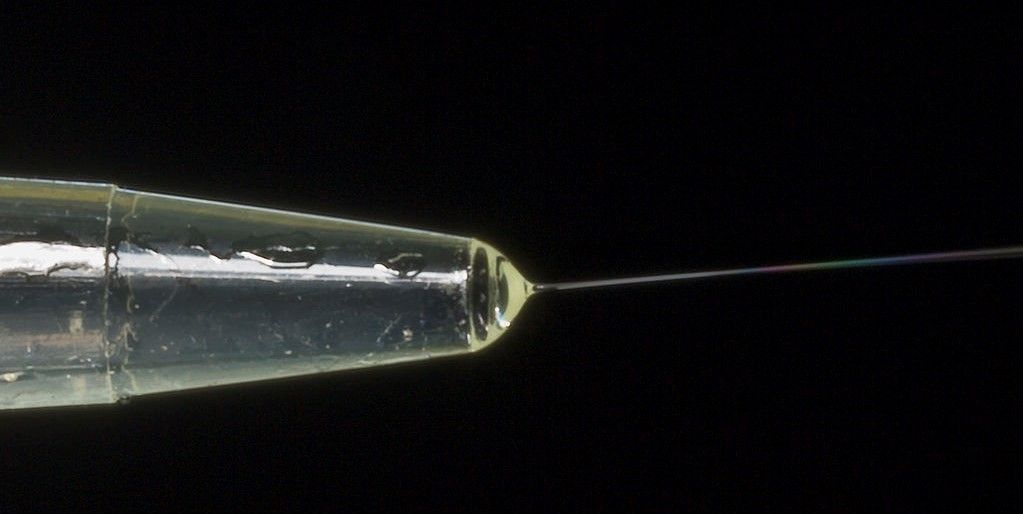
The most astounding part of nanoparticles is the impact they can have despite, or even because of, their small size. Measuring less than 1/100ththe size of a human red blood cell enables nanomaterial specialists to add them to a variety of products without affecting any of the original, desirable properties. This means that they can be used in the manufacture of large products such as car tyres, polymer flooring systems, or polycarbonate sheeting, as well as in the production of very fine materials, such as miniature electronic devices or electrospun fibres.
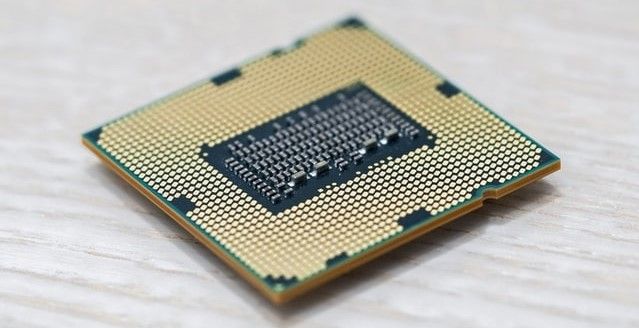
On a practical level, nanoparticles are often delivered in the form of a nanosuspension – a liquid which contains nanomaterials.
Different nanomaterials are used to gain different properties in the final product. For example, nanoparticles of silver can provide biocidal properties to a polymer, while carbon nanotubes can boost mechanical performance or add electrical conductivity.
As the range of materials used (silver, gold, carbon, copper…) and the nanoscale form they are given (single-walled tube, multi-walled tube, 2D sheet, ball, particle …) is so varied, the range of potential properties is also far-reaching. Chemical resistance, thermal conductivity, added strength, UV-protection, electro-magnetism, antibacterial properties, and even electroconductivity, are all possible benefits from using nanomaterial additives.
After years of perfecting these properties in the lab, the use of nanomaterials in commercial electrospinning processes is now possible.
Developed by nanomaterial scientists, NANO AB PA6 is a silver nanoparticle colloid solution based on a concentrated formic acid which provides stable antibacterial properties to electrospun fibres. It is a solution for industry provided by the nanotechnology experts at NANO CHEMI GROUP and is made up of nanoparticles measuring up to 40 nm in size which have been dispersed in formic acid with a concentration of 98-99%.
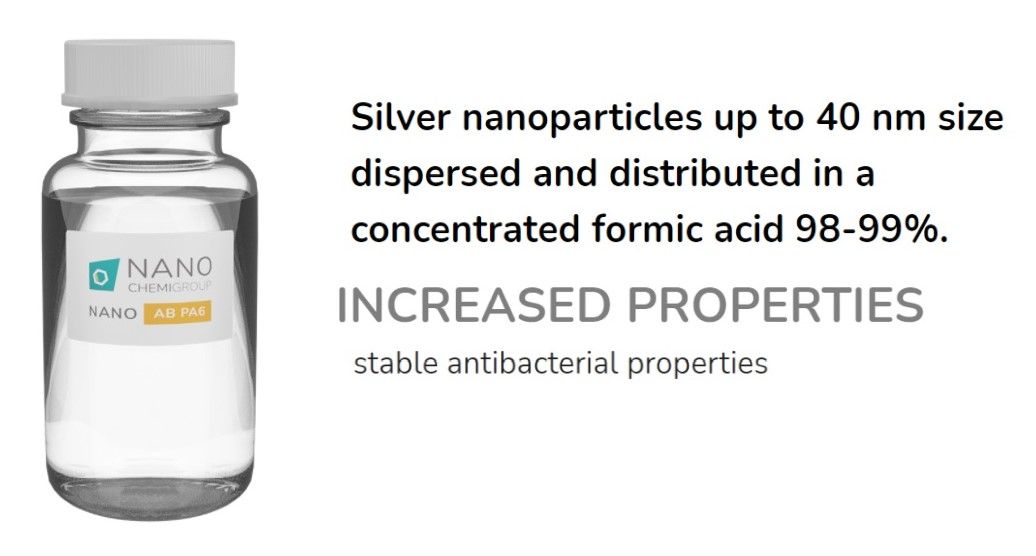
The process for applying NANO AB PA6 is highly specialised, although full technical support is provided by NANO CHEMI GROUP’s experts. However, in layman’s terms, the original polymer is melted and diluted with the nanosolution. A chemical composition is then used to return the polymer back into a solid state, or the acid is simply evaporated away, to allow an even integration and distribution of the nanoparticles throughout the polymer.
The nanosolution can also be based on non-acidic liquids if required.
Nanoparticle suspensions, such as NANO AB PA6, are in high demand not only due to their easy application, but also because they are so effective. Just a small amount of nanomaterial product is needed to make desired changes, making them suitable for even the thinnest fibres.
While NANO AB PA6 provides an antibacterial property for manufacturers of non-woven synthetic fibres (such as those used in medical masks, respirators, and medical clothing), other nanotechnologies can be provided.
Electrospinning is a practical production process for modern polymers, but now nanotechnology can now provide these materials with even more unique selling points.
Photo credit: NANO CHEMI GROUP, Robert Lamberts, & Jeremy Zero on Unsplash