A team of chemists from Rice University have developed a cleaner and cheaper way of producing syngas by using nanotechnology.
The new process is cheaper because it uses less energy, which also makes it more environmentally friendly. Given the versatility of syngas (synthesis gas) as a raw material and feedstock for a wide range of chemical products, such as ammonia for fertilizer, for fuel and for producing methane, the discovery could have a major impact on reaching climate change targets.
Syngas is made by a process called gasification of a carbon containing fuel, such as coal emissions, steam reforming of coke, or waste emissions from burning natural gas or biomass for energy. It is a mix of carbon monoxide and hydrogen gas that is used to make chemicals and fuels with a value, according to BCC Research, of more than $46 billion per year.
The breakthrough was made at Rice University in Texas, where researchers discovered that nanoparticles of copper dotted with single atoms of ruthenium can work as a more efficient catalyst than current methods.
“Syngas can be made in many ways, but one of those, methane dry reforming, is increasingly important because the chemical inputs are methane and carbon dioxide, two potent and problematic greenhouse gases,” said Naomi Halas, one of the study’s co-authors.
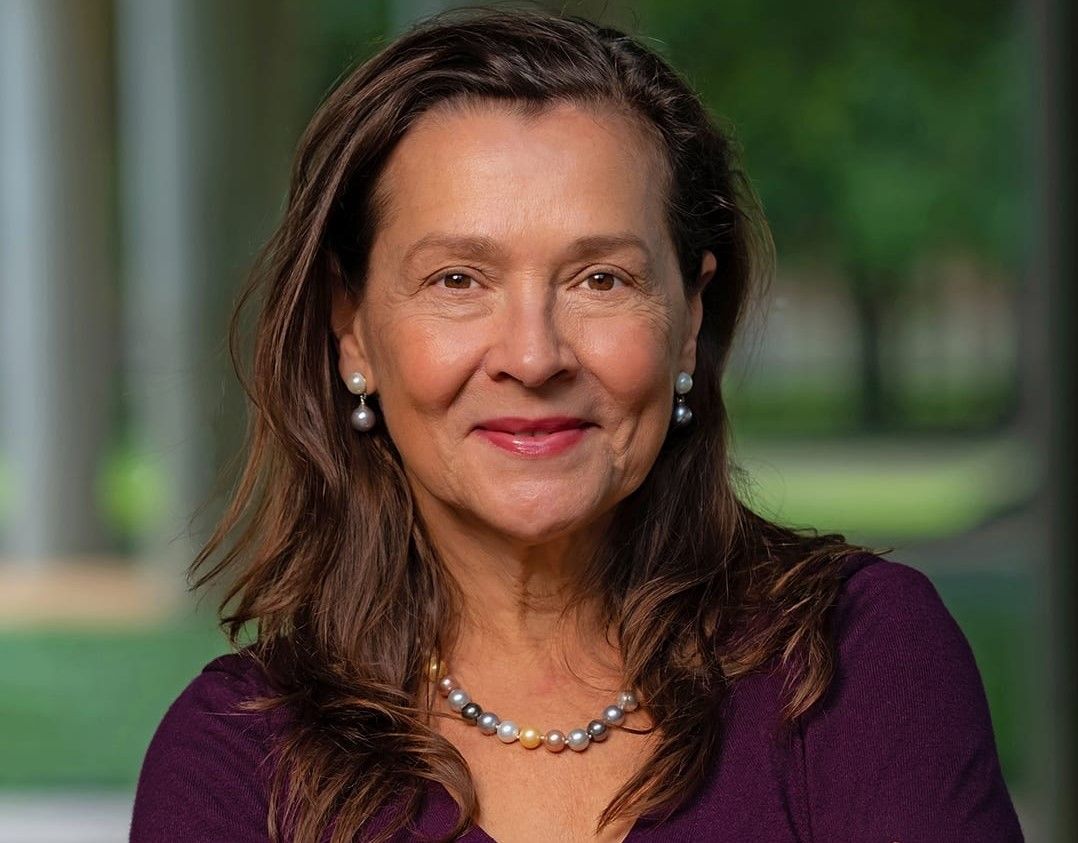
Gasification requires catalysts to encourage the chemical reactions that break apart the hydrocarbons to make syngas, typically using steam as a source of energy.
As the online journal Science Daily notes, “The hydrogen atoms pair up to form hydrogen gas, and the carbon atoms combine with oxygen in the form of carbon monoxide. In dry reforming, the oxygen atoms come from carbon dioxide rather than steam.”
The problem, explains the study’s first author Linan Zhou, a researcher at Rice’s Laboratory for Nanophotonics (LANP), is that, “… dry reforming hasn't been attractive to industry because it typically requires even higher temperatures and more energy than steam-based methods.”
Solving the challenge took many years of study. As the Rice University press release outlines, “Halas, who directs LANP, has worked for years to create light-activated nanoparticles that insert energy into chemical reactions with surgical precision. In 2011, her team showed it could boost the amount of short-lived, high-energy electrons called ‘hot carriers’ that are created when light strikes metal, and in 2016 they unveiled the first of several ‘antenna reactors’ that use hot carriers to drive catalysis.”
In a 2018 study, the team found that a copper and ruthenium antenna reactor could produce hydrogen from ammonia – a process that was the basis for the syngas discovery.
In each catalyst, the press release reports, “a copper sphere about 5-10 nanometers in diameter is dotted with ruthenium islands. For the ammonia catalysts, each island contained a few dozen atoms of ruthenium, but Zhou had to shrink these to a single atom for the dry reforming catalyst.”
“High efficiency is important for this reaction, but stability is even more important,” says Zhou. “If you tell a person in industry that you have a really efficient catalyst they are going to ask, ‘How long can it last?’”
For example, most gasification catalysts suffer from ‘coking’, where carbon builds up on the surface rendering them useless. This would require syngas producers to add fresh catalyst raw materials, increasing costs.
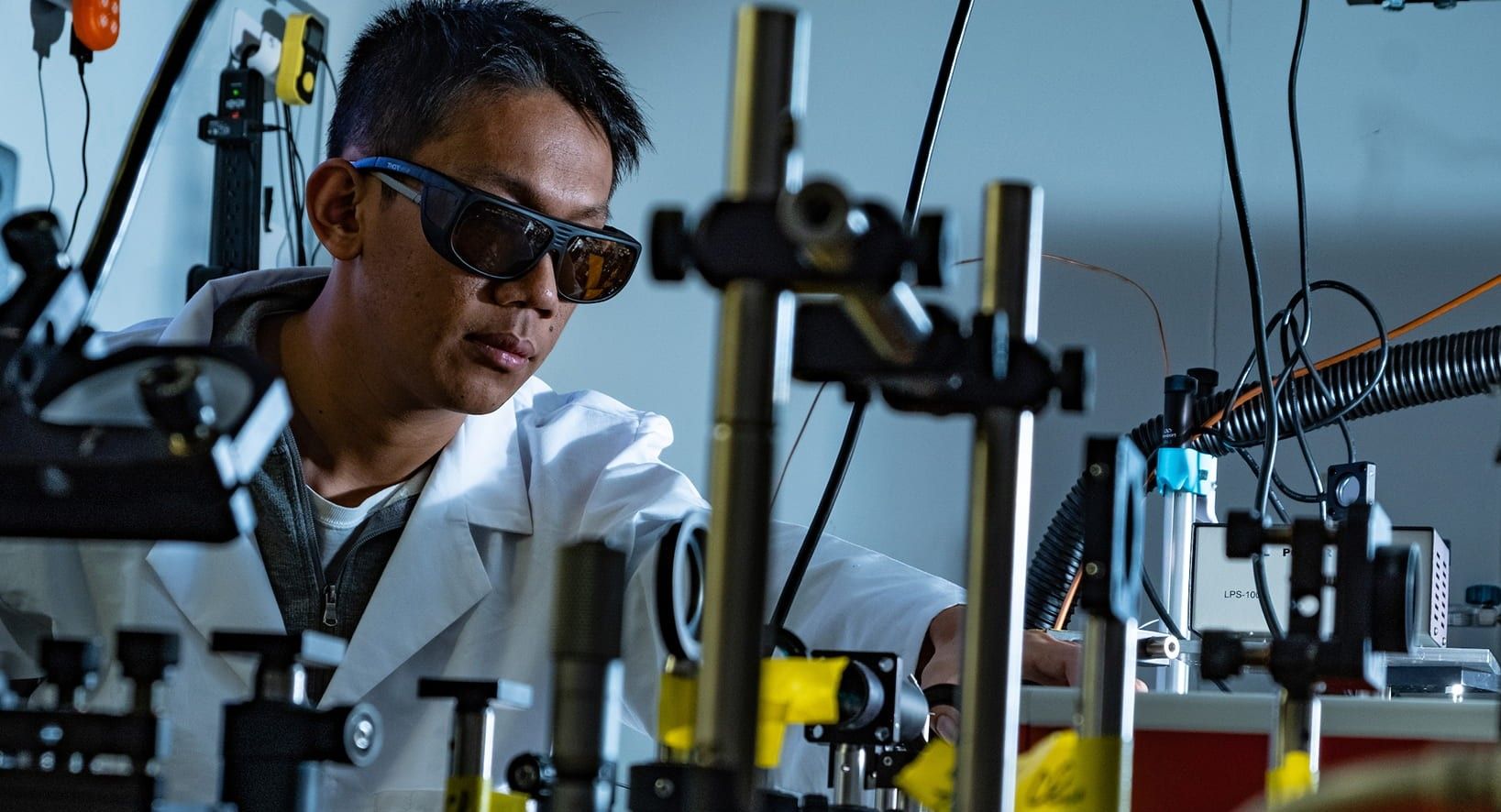
“They [producers] cannot change the catalyst every day,” says Zhou. “They want something that can last.”
The new process reduces the chances of coking by isolating the active ruthenium sites where carbon is dissociated from hydrogen, allowing them to more freely react with oxygen to form carbon monoxide.
“But single-atom islands are not enough,” adds Zhou. “For stability, you need both single atoms and hot electrons.”
For this reason, the team analysed how hot carriers reacted with the hydrogen, finding that it often drove the atoms away from the reactor surface.
“When hydrogen leaves the surface quickly, it's more likely to form molecular hydrogen,” he notes. “It also decreases the possibility of a reaction between hydrogen and oxygen, and leaves the oxygen to react with carbon. That's how you can control with the hot electron to make sure it doesn't form coke.”
The result is a cheaper and cleaner way to produce syngas, with a lower carbon footprint than current processes.
While further work is needed to ensure that the technology is up scalable, Halas believes that the method is ideal, “… for sustainable, light-driven, low-temperature, methane-reforming reactions for production of hydrogen on demand.”
However, the use of single-atom antenna-reactors could even have uses beyond syngas production. With catalysts employed across the chemical industry for a multitude of uses, the development of a novel energy efficient catalyst made from nanoparticles is certain to attract interest.
Further evidence, if needed, of the growing power and range of applications for nanomaterials.
Photo credit: RiceUniversity, Kraftworkfurschung, & Gasworld.