As demand for nanomaterials continues to grow, so too has the size of the market and the number of nanoproduct manufacturers and suppliers.
In fact, the market is now so mature, and the technology so well developed that production has begun in less obvious places.
One example of this is how researchers at the National Chemical Laboratory (NCL) in Pune, India have developed an inexpensive approach to manufacturing silver nanowires. A low-cost, continuous flow method that has recently established a pilot plant. If the correct investment follows, the facility and others like it promise to supply precision nanomaterial products for India’s rapidly expanding technology industry.
With nanowires now being used in a wide range of electrical goods, such as touchscreens, infrared shields, and conductor inks used in electronic circuit manufacturing, it is likely that projects like this are just the beginning for mass production of nanomaterials outside of G7 countries.
While the technology is not new, what is different is the way that it has been applied, specifically focusing on keeping costs low.
“The method of this synthesis is known chemistry, but it was possible using different control parameters in the lab,” said Dr Amol Kulkarni, lead researcher at Chemical Engineering and Process Development Division, NCL. “The purpose was to create a technology that will compete in the world and get into the field of electrical chemicals.”
Dr Shekhar Mande, the Director General of the Council of Scientific and Industrial Research (CSIR), agrees, announcing at the pilot plant’s opening ceremony how, “With the help of this technology … Indian industries will be able to enter into the manufacture of electronic chemicals.”
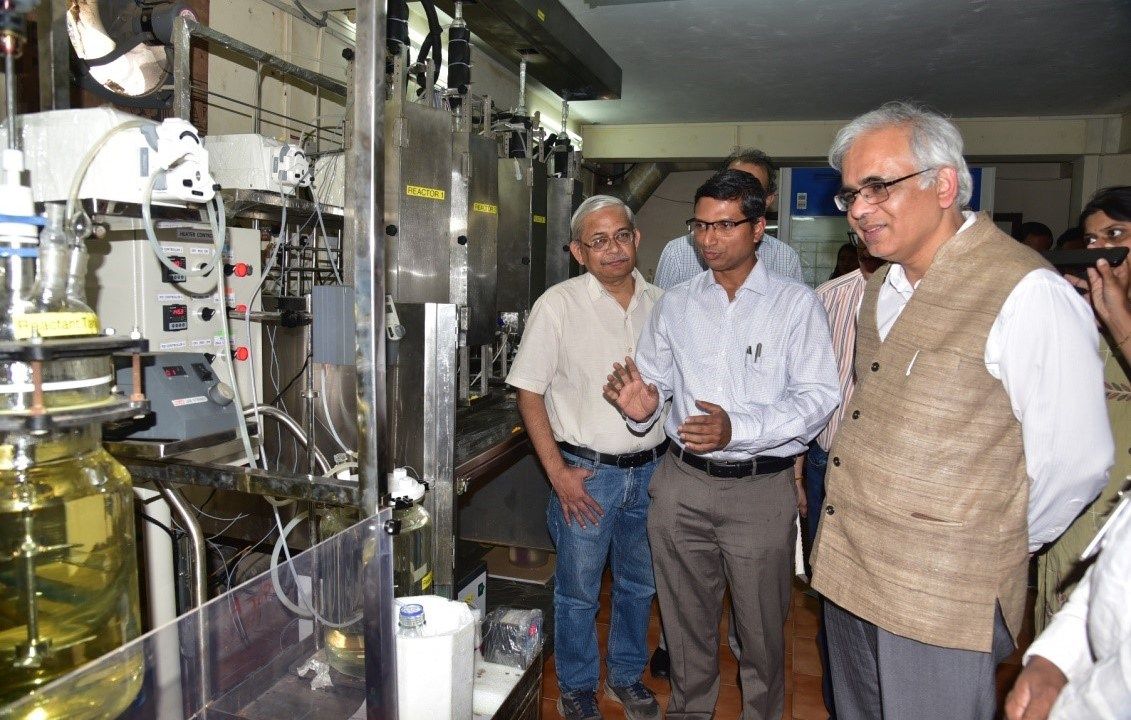
This optimism is based on the developers’ belief that they can produce high-quality silver nanowires 12 times cheaper than prices on the current market.
“The price for silver nanowires of different sizes (20mm to 100mm diameter) varies from $250 to $600 per gram while the ones manufactured by NCL cost $18 per gram,” reports the Times of India. Adding that, “The pilot plant at CSIR-NCL can produce as much as 500 grams a day and is scalable to any desired production rates. Also, the process can be adjusted to manufacture a wide range of nanowires suitable for a variety of applications.”
At present, India imports all of the silver nanowires that its enormous mobile phone production sector requires. The hope is that this pilot plant will prove successful enough in terms of price and quality to help meet some of this demand with locally produced raw materials.
As the Economic Times of India noted in August 2019, “[The growth] From just two manufacturing units back in 2014 to 268 mobile handset and accessories manufacturing units in 2019 has led to 95% of mobile phones sold in the country being produced domestically. In fact, India is today the second-largest mobile phone manufacturer in the world after China.”
“India has achieved tremendous success in mobile phone and component manufacturing in the last four years,” observes Panjak Mohindroo, the Chairman of the India Cellular and Electronics Association (ICEA). “Our domestic market viz-a-viz manufacturing is saturated, and we have set our sights on a target of Rs 7.7 lakh crore of exports by 2025.”
This equates to an export target of almost $108 billion of the predicted $2,300 billion smartphone market in just five years’ time. In comparison, global mobile phone sales in 2018 totalled $520 billion.
But even without such exceptional growth in the mobile phone market, demand for electronic components and the nanomaterials to make them is expected to increase rapidly over the next decade.
At present, India domestically produces only a few inorganic oxides such as titanium dioxide and carbon nanomaterials. However, the nanomaterial manufacturing sector is developing quickly, often with novel nanoproducts, such as nanoscale metal mesh technologies. Meanwhile the range of applications for nanomaterials is growing, so that they can now be found in multi-touch screens, polymer-nano composites, nanoceramic dental implants, filters for optical components, antimicrobial coatings, nano-diaphragms for acoustic sensing, and medical sensors.

“The global market for the silver nanowires is very large,” observes Dr Mande. “There are ample opportunities for nanowire manufacturers as there are very few producers in this sector.”
Additionally, “Nearly one in every four nanotechnology professionals in the world is likely to be an Indian for the decade ending 2025,” according to an Assocham-TechSci Research joint study.
“In recent times, silver nanowires have caught attention due to their suitability for printed and flexible electronics. It is used in tightly controlled markets where India has almost zero footprint,” said an NCL spokesperson. “Now, with this technology developed at CSIR-NCL, Indian industries will be able to enter into the manufacturing of this precision material.”
Such is the contrast of the nanomaterial industry. While business is based on raw materials that are incredibly small, the market for nanomaterials certainly isn’t.
Photo credit: Researchstash, BGR, Electronicsforu, Countryflags, & Greenbergtraurig.